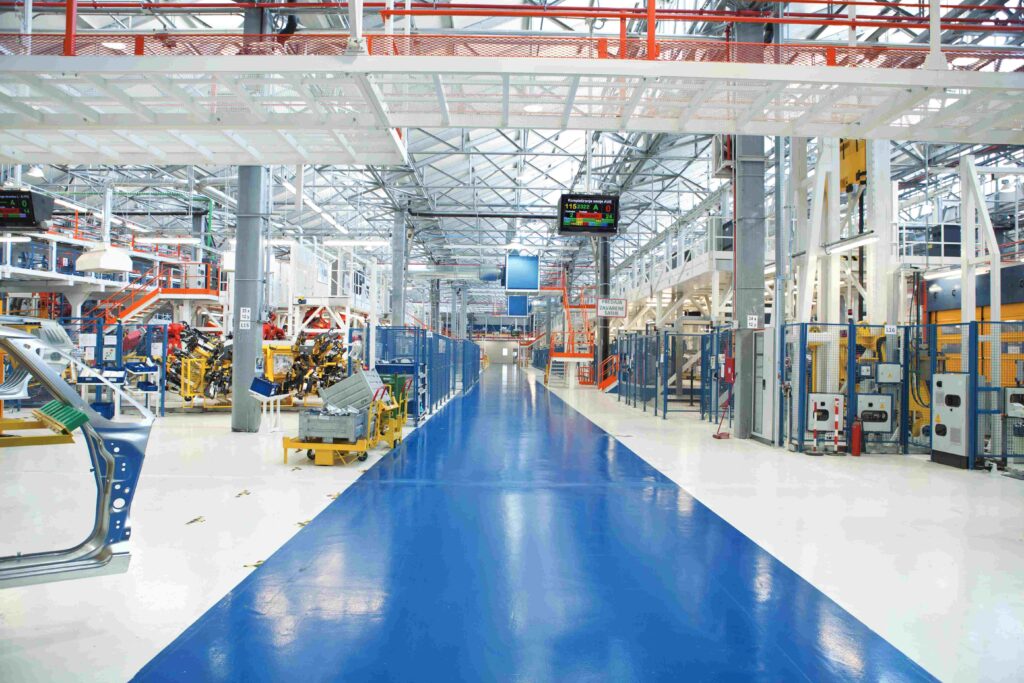
A targeted poll of 120 professionals — including facility heads, plant managers, hygiene experts, and service providers — unveils the dynamic shifts and pressing challenges defining Facility Management across industrial sectors. The results highlight key concerns surrounding hygiene, compliance, sustainability, technology adoption, and workforce development. With expert commentary anchoring the findings, this cover story dives deep into the current state of the industry and reveals the pivotal trends and innovations shaping its future.
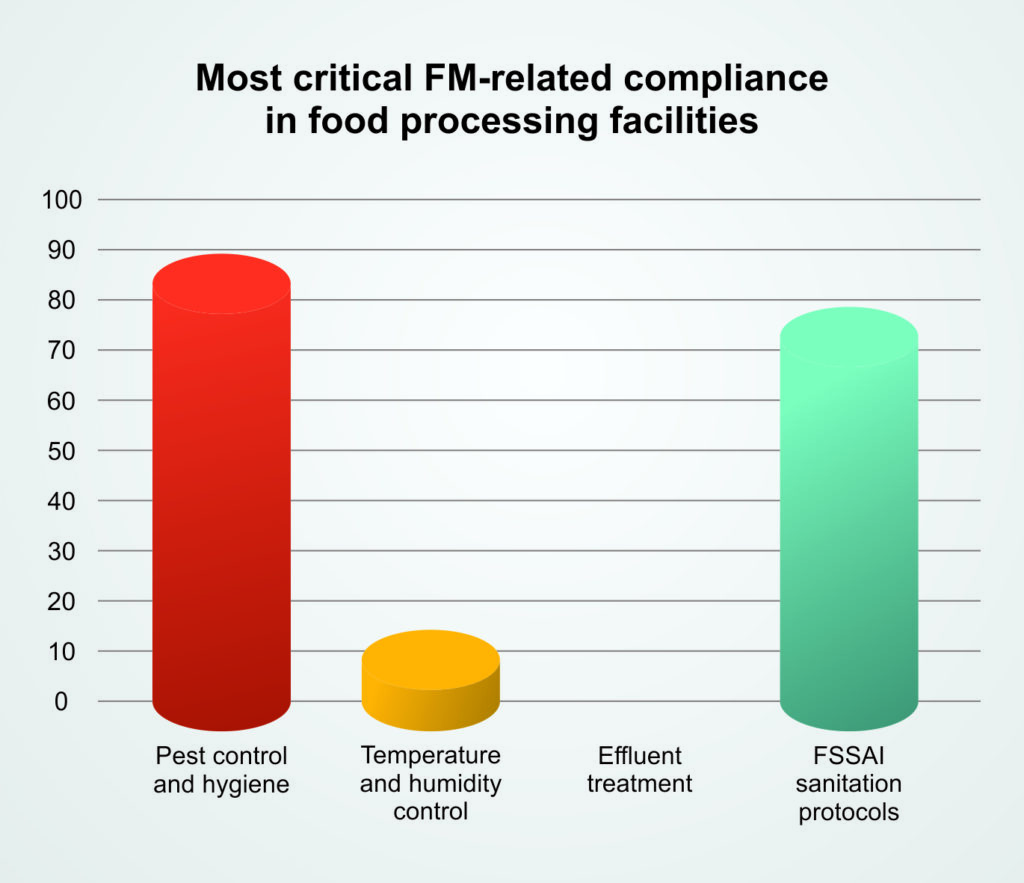
1. What is the most critical compliance requirement in food processing facilities?
Cleanliness and hygiene of a food processing facility is paramount. And facility managers are most concerned about pest control and hygiene, making it the most critical compliance requirement, as was voted by 87% of the respondents. This was followed by FSSAI sanitation norms. Temperature/humidity control and effluent treatment were less prioritised.
With the increase in food consumption and processed foods, FM has an extremely vital role to play in ensuring sanitation protocols are met. Experts say regulatory guidelines are already in place for FSSAI, HACCP and food safety management. However, how to meet those standards through improved and scientific cleaning methods is a learning process for most FM professionals. They need to go beyond the basic understanding of hygiene.
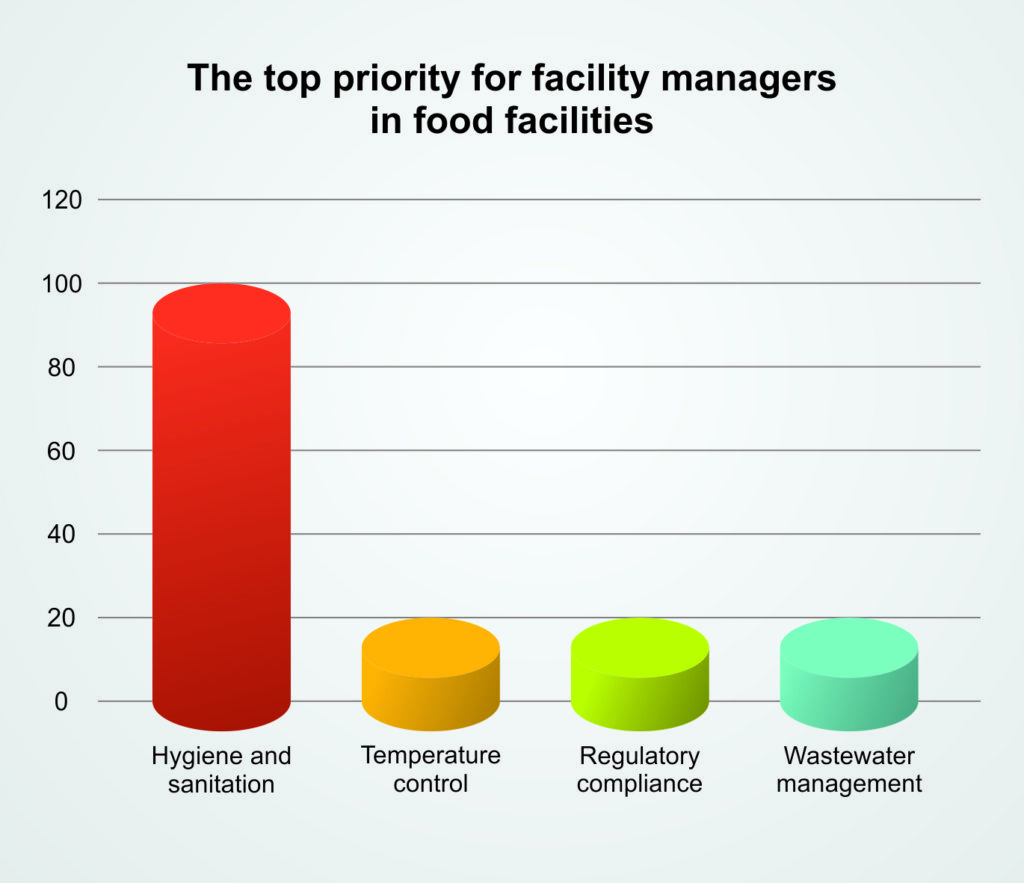
2. What is the top operational priority for facility managers in food facilities?
The hygiene and sanitation of the food facility, including that of the workers, machinery and the surrounding area, is the top priority of the facility managers. In the poll, 100% of the respondents voted for hygiene and sanitation. Temperature control and regulatory compliance followed.
In food facilities, “Hygiene and sanitation” is a broad term. “It involves quality of drinking water, contamination in raw materials, cleanliness of floors, walls, ceilings, doors, windows, kitchen tools, waste handling, light fittings, refrigeration, etc. Hence, operationally, this remains a big challenge,” said a quality assurance manager of a food company.
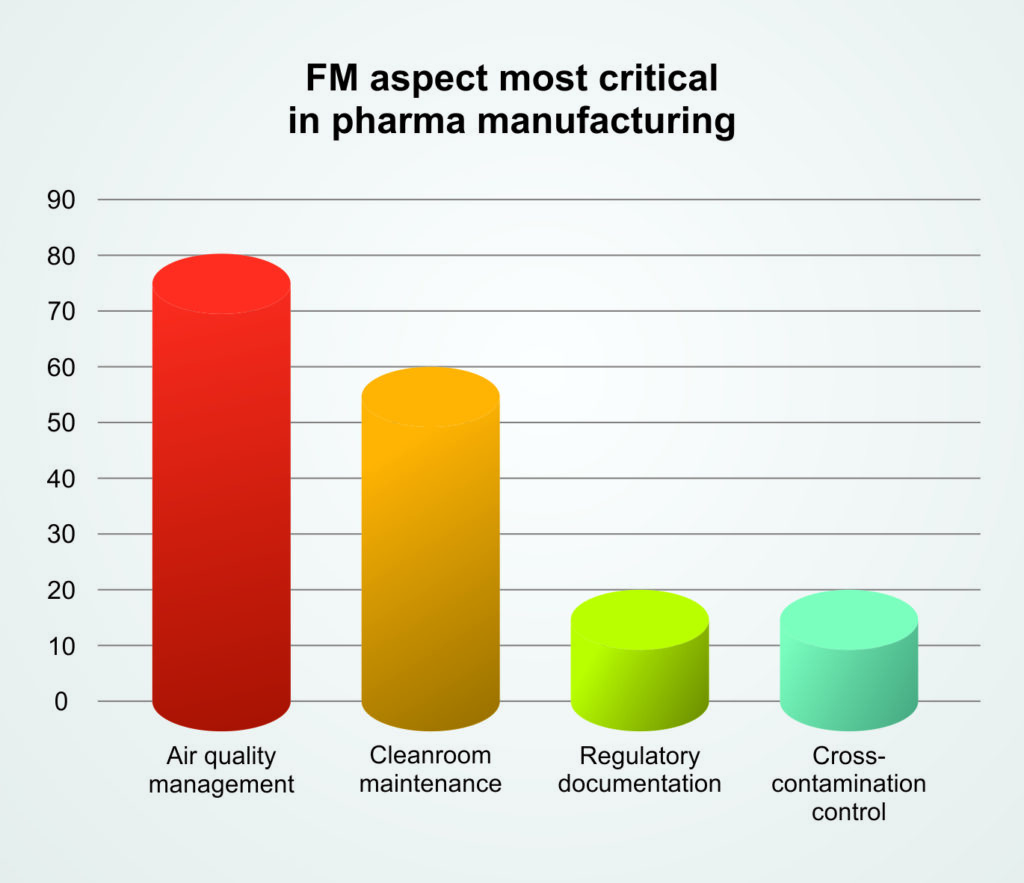
3. Where should regulatory focus lie in pharma and cleanroom environments?
According to 80% of the respondents, air quality management is the key focus in cleanrooms. 60% also said that maintenance of the cleanroom is a regulatory requirement, which is a part of the audit. But they do not consider documentation a part of FM and hence, voted less for documentation.
According to experts, air quality has become a concern in both hospitals and pharma manufacturing units. In fact, lack of awareness about pharma-specific and industrial cleaning in FM is a big concern. Some feel that pharma companies should have a separate FM department to manage hygiene protocols.
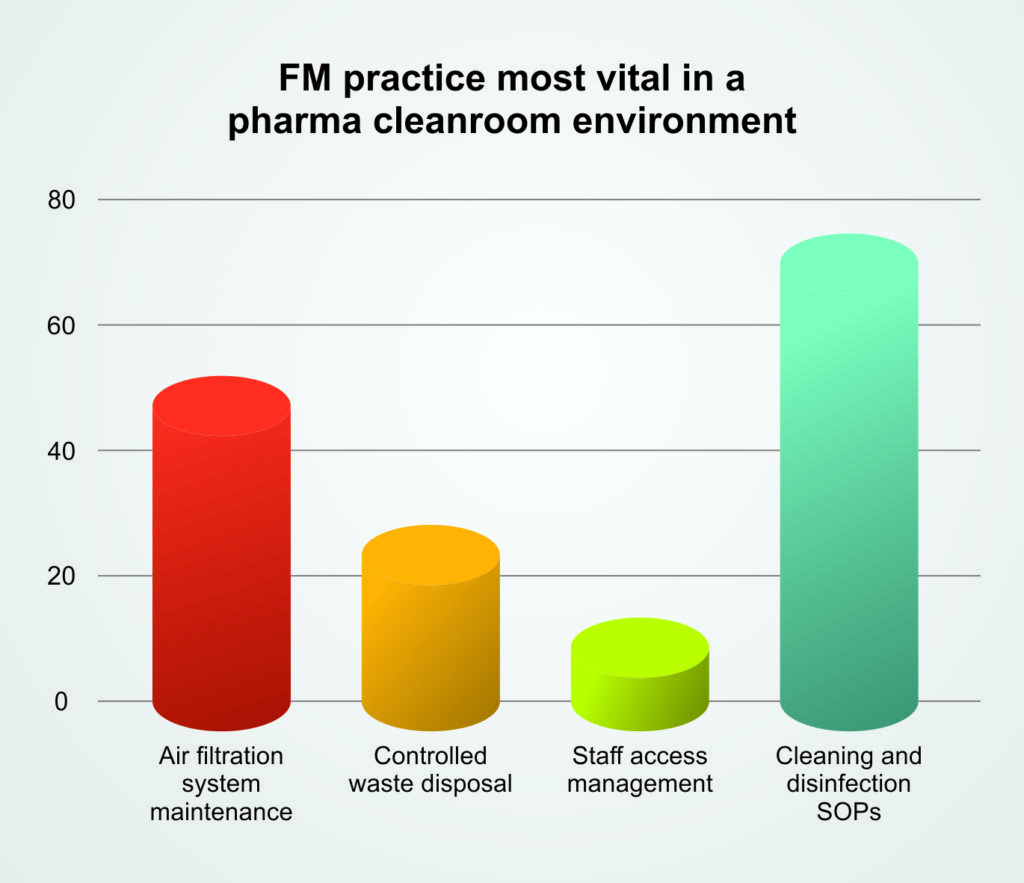
4. What is the most crucial operational need in cleanroom facilities?
Respondents voted air filtration system maintenance as the most crucial operational need in cleanrooms. Waste disposal, access control and air shower maintenance followed. In a cleanroom environment, if the air filtration system is not maintained properly, the entire production cycle can get contaminated.
According to pharma cleaning experts, there is very little awareness among FM heads regarding the maintenance of AHUs, ducts, filters, etc. There are different filters for different areas, depending on the product manufactured and the level of contamination risk. Experts recommend a detailed SOP, schedule and documentation of every aspect of air filtration maintenance in pharma plants.
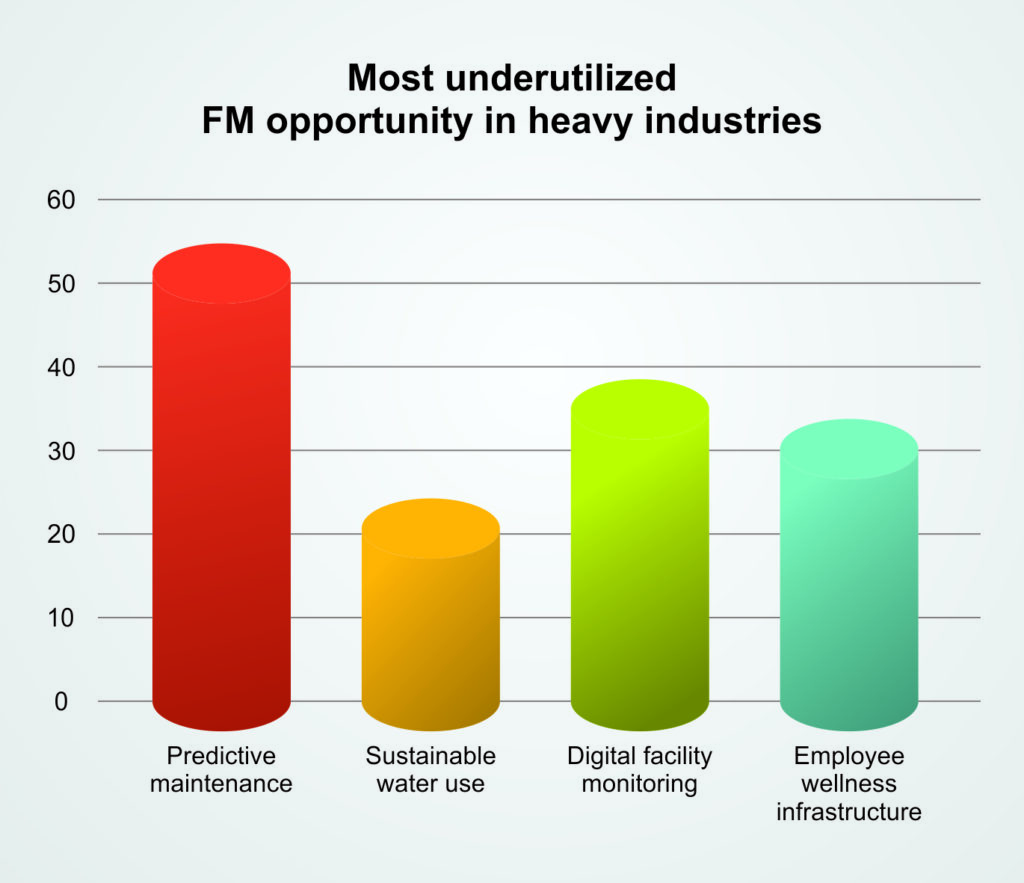
5. Which future-ready initiative is most relevant to FM today?
Most facilities still operate on reactive maintenance, said experts and hence predictive maintenance is being increasingly adopted by hospitals, manufacturing units and large facilities. Over 53% of the respondents voted for predictive maintenance. This was followed by digital monitoring, water sustainability and emission tracking.
Digital monitoring is helping FM professionals to plan equipment usage, optimise productivity and set up maintenance schedules. Predictive maintenance is capital intensive, but in the long run, it saves cost and downtime. Emission tracking is primarily a plant function and FM professionals have limited role in that space.
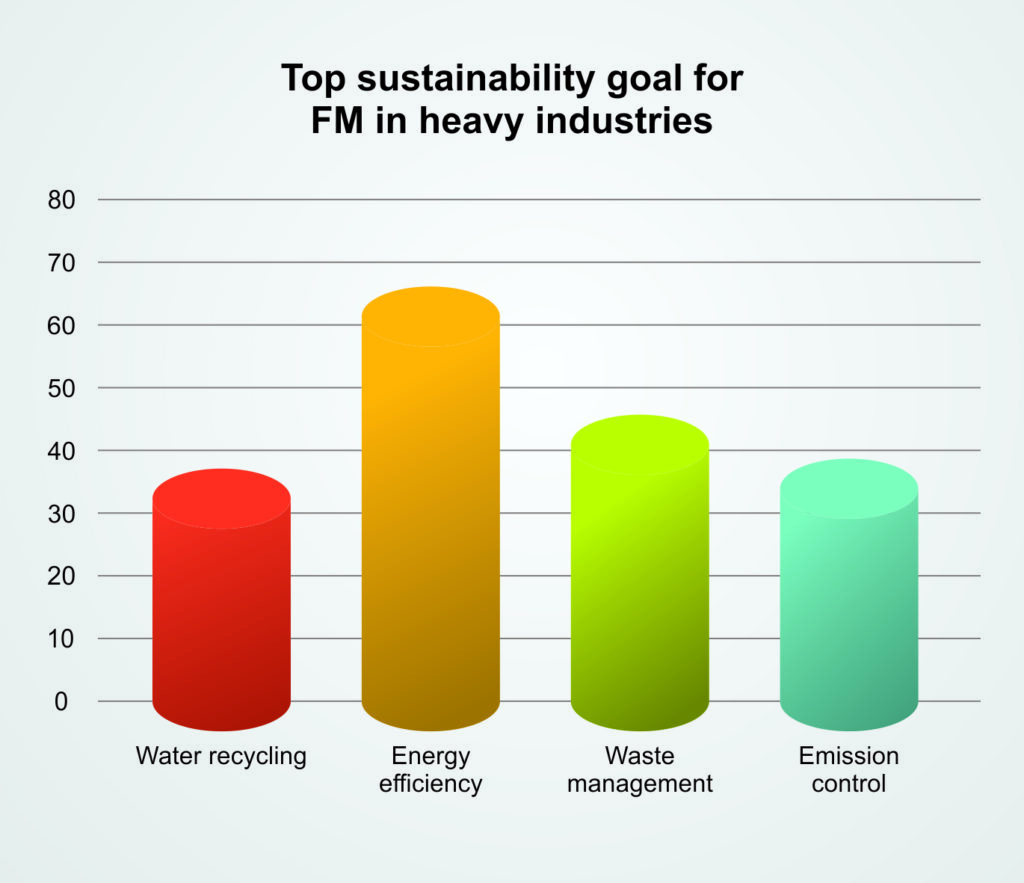
6. Which sustainability area is FM most invested in?
Energy efficiency is on top of the sustainability agenda of FM, as voted by 67% of respondents. Water recycling and solid waste management are also being implemented. Emission control and green product usage are slowly catching up.
According to FM experts, energy savings is largely applicable to commercial buildings and offices, where lighting, HVAC and power usage can be planned better. But in heavy industries like steel or pharma, FM plays a very limited role in energy savings. Similarly, waste management is more about disposal and documentation than about planning and recovery. But the awareness has increased, say experts.
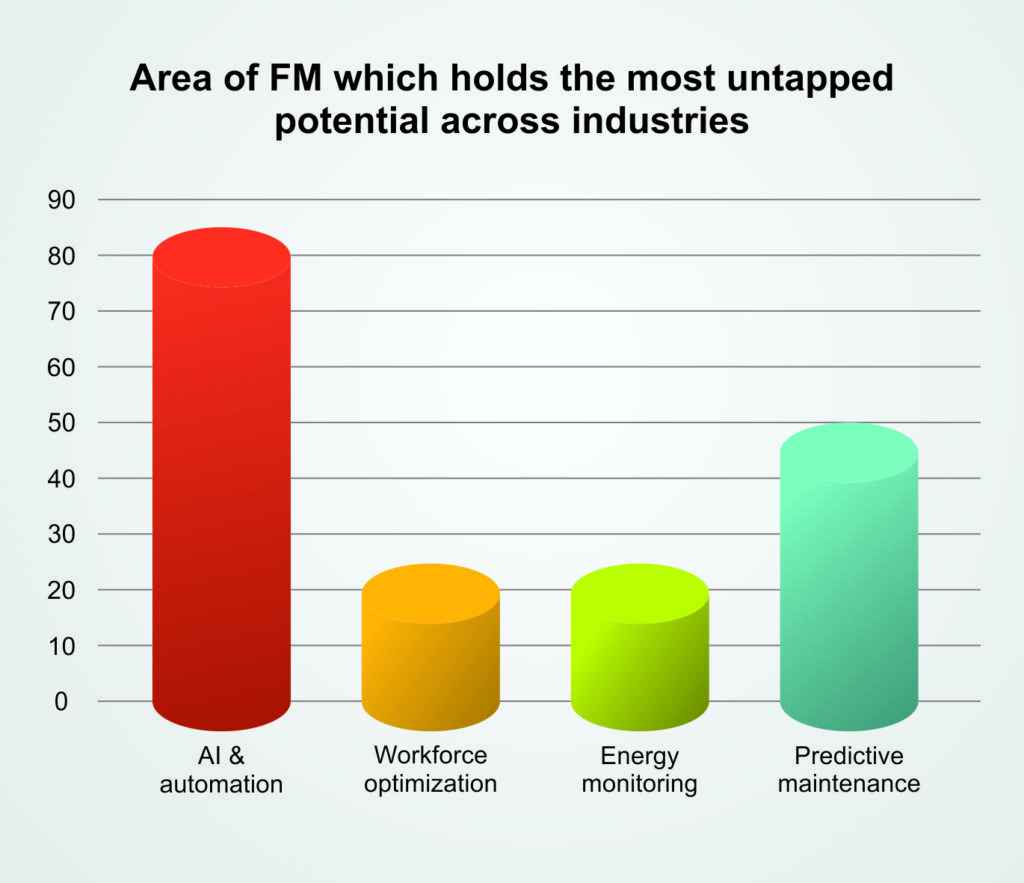
7. What is the most underutilised FM technology today?
FM experts say that although digitisation is a buzzword, its usage is still limited to tracking and documentation. About 83% of the respondents voted for AI and automation, saying that it is the most underutilised technology in FM. Workforce management and sustainability tools followed.
The future of FM lies in automation. But at present, FM is more focused on energy management and preventive maintenance. AI and robotics will follow, once the facility reaches a level of standardised quality and compliance.
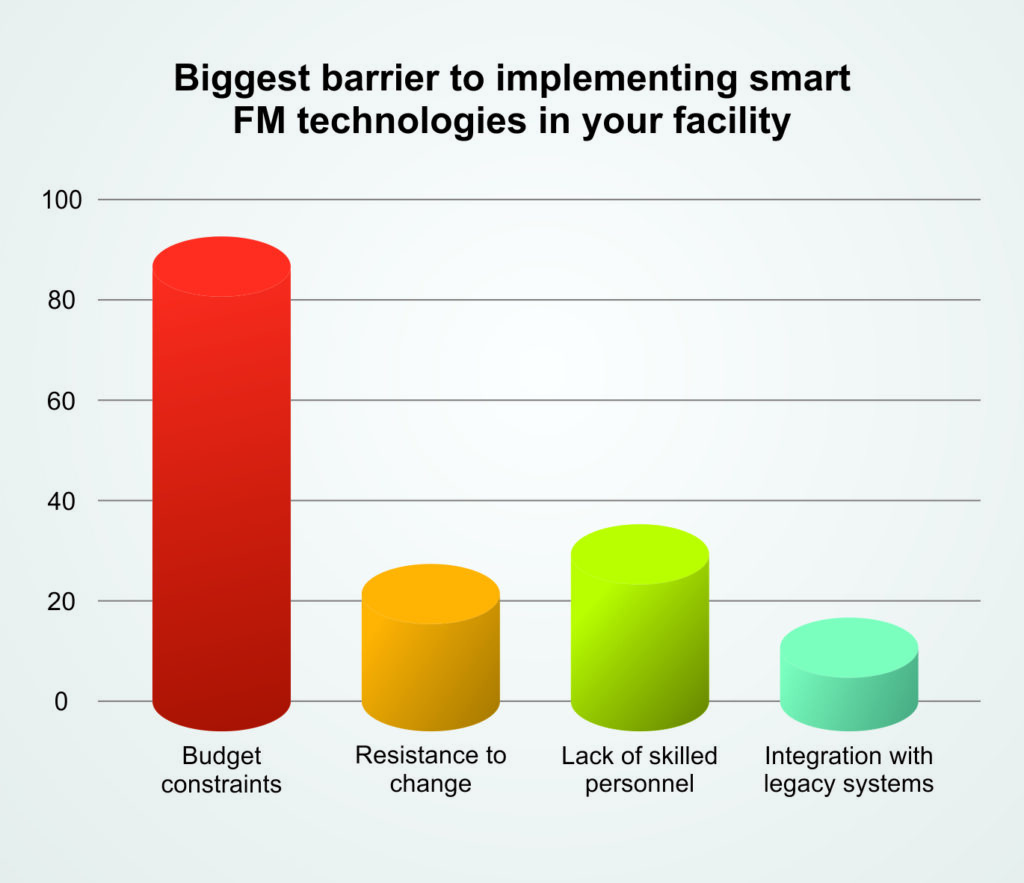
8. What is the biggest barrier to FM tech implementation?
Over 91% of the respondents said that budget is the biggest hurdle in adopting FM technology. Shortage of skilled manpower and resistance to change are also factors.
According to industry leaders, FM tech takes a backseat because of the capital cost involved and the difficulty in integrating it with existing systems. Moreover, most FM companies are not comfortable with data sharing and open platforms and worry about breach of information. There is also a lack of understanding of ROI. Some FM software solutions are now available on SaaS platforms and OPEX models, which can bring down costs.
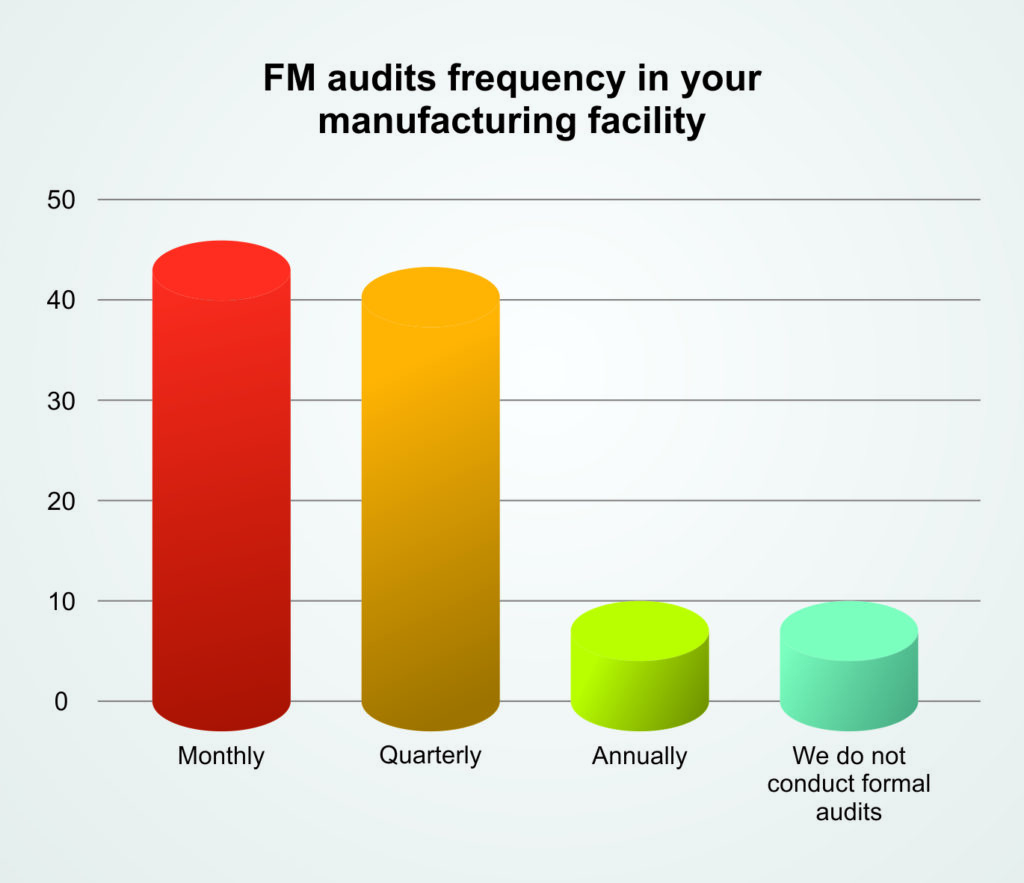
9. How often should facility audits be conducted?
About 43% of the respondents said that monthly audits are necessary. Quarterly audits (41%) and annual audits (13%) were also voted. Facility audits are like health checkups of an industry. If the audits are regular, any risk of contamination or breakdown can be identified at an early stage. However, experts feel that there is a strong need for third-party audits because internal FM audits do not highlight the problems.
Monthly third-party audits, in fact, bring out a lot of minor issues that FM teams fail to capture. Seasonal audits are also important, especially in food industry.
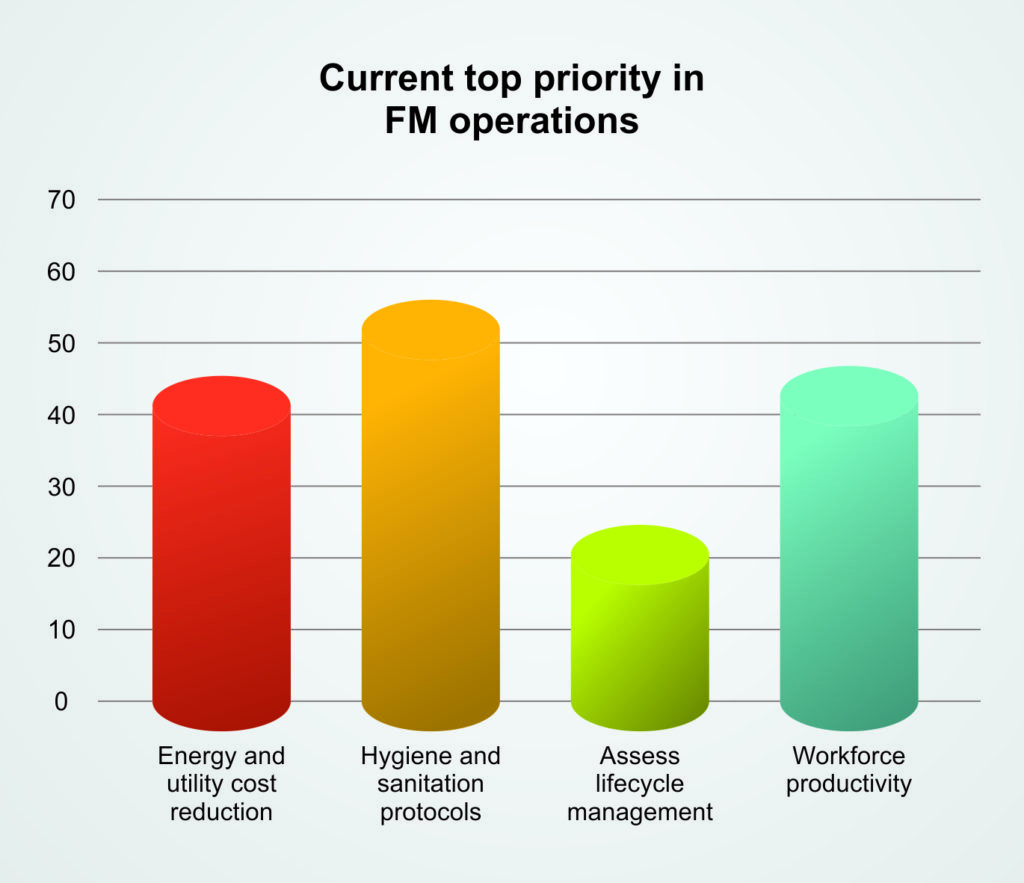
10. What is the most strategic priority for FM?
Hygiene and sanitation protocols were voted by 58% of the respondents as the top strategic priority in FM. Cost control and lifecycle assessment followed. This reflects what is happening on ground.
The biggest challenge today in industries is to meet the basic hygiene requirement of the facility. Once that is in place, the company can look at improving performance, saving cost and implementing ESG goals. If the facility is not hygienic, it affects brand reputation and growth.
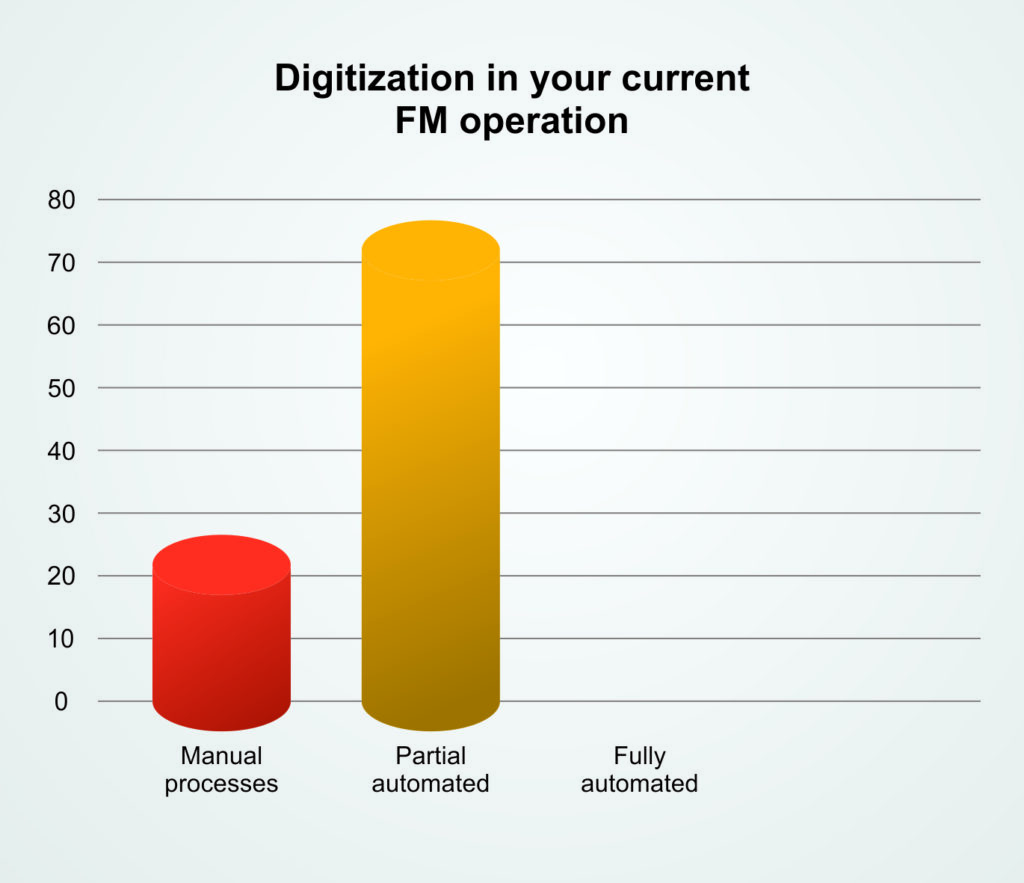
11. What level of automation exists in industrial facilities?
Most industrial facilities have partial automation, say respondents (75%). Only a few facilities have complete automation (15%). Manual operations are still in use in 26% facilities. This gives us a real picture of the ground reality. Full automation is only seen in high-end pharma, semiconductor and automobile plants. But now, most of the new equipment is coming with SCADA, sensors and cloud connectivity.
The user interface has become very simple. In fact, future equipment will come with AI and image-based analytics. So, the FM team needs to understand and operate these technologies.
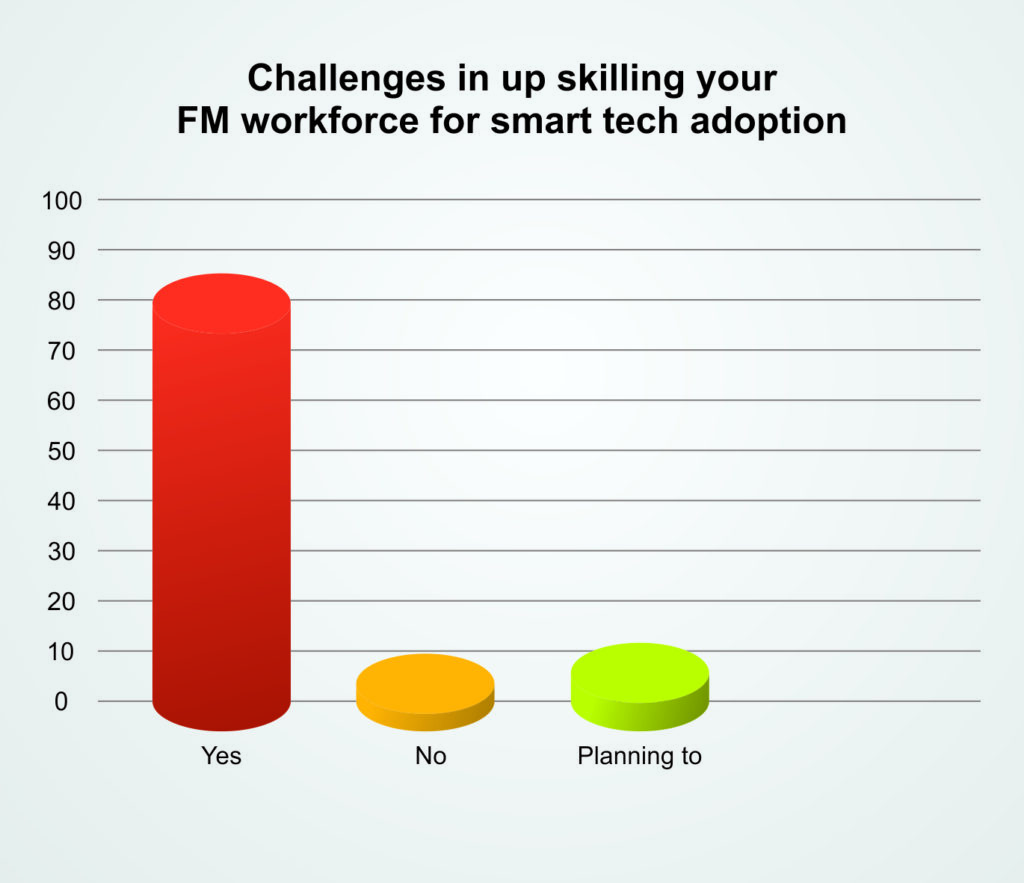
12. How important is upskilling in FM?
Over 81% of the respondents said that upskilling is very important. Another 10% said that they are planning to upskill their team. FM experts say that upskilling and training is very important in FM, because the industry is growing, but trained manpower is not available. Once a staff is trained, he is poached by other companies. Therefore, there is a need to train, upskill and retain. Training should also be extended to supervisors and ground staff and not limited to facility heads.
The poll results highlight several key trends that will shape Facility Management (FM) strategies across sectors. Hygiene and sanitation continue to be top priorities, underscoring their critical role in compliance and brand reputation, especially in food processing facilities. This signals a shift toward considering hygiene not just as a maintenance task but as a strategic necessity. In the pharmaceutical and cleanroom sectors, air quality management remains a top focus, with experts stressing the importance of upgrading systems to ensure contamination-free environments.
The data also emphasizes the growing importance of predictive maintenance and AI-driven automation. Despite the clear benefits, FM heads face budget constraints and resistance to technological integration. To overcome these hurdles, facility managers will need to demonstrate the long-term value of such investments, including reducing downtime and operational costs. The increased adoption of predictive maintenance and digital monitoring, however, shows a promising move toward more proactive management.
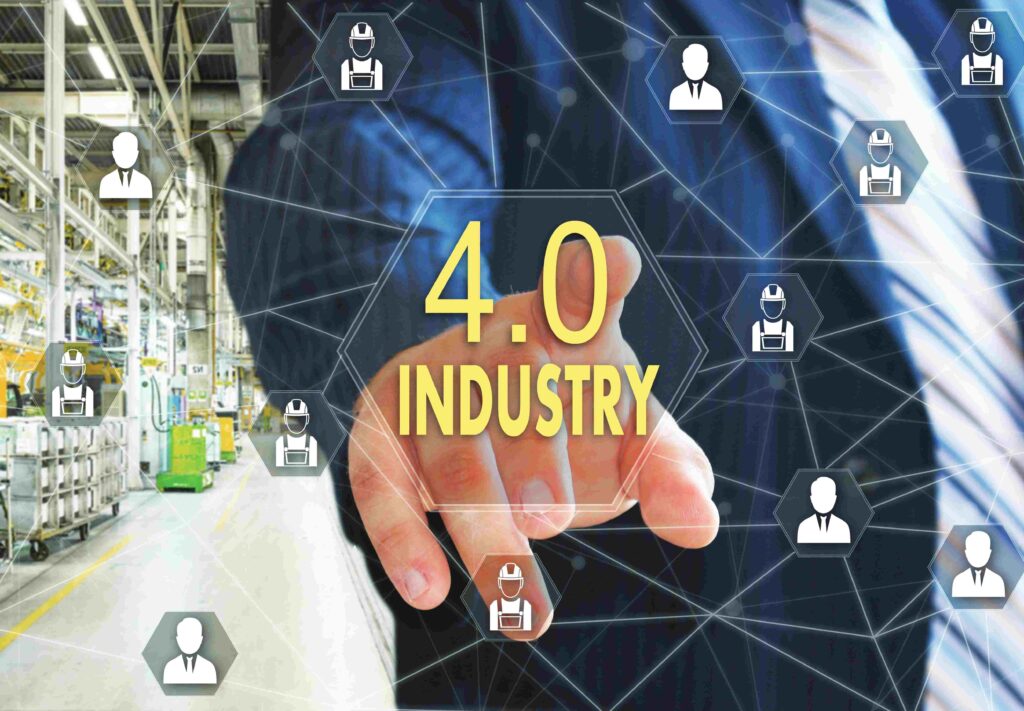
Sustainability is becoming an increasingly important agenda, with energy efficiency taking centerstage. While water recycling and waste management are also gaining attention, they are still seen as secondary priorities. The industry is slowly aligning with ESG goals, but there is still a need for more comprehensive approaches to environmental sustainability.
Additionally, upskilling the FM workforce is recognized as vital, but challenges such as high attrition rates complicate this effort. The poll results highlight a critical need for training programs that also focus on retaining skilled personnel, a balance that FM leaders must address for future success.
Ultimately, the poll underscores that while FM heads across sectors recognize the importance of technology, sustainability and skilled labour, the path forward requires overcoming significant operational and financial challenges. By investing in strategic upgrades, fostering innovation and focusing on people, facility management will continue to evolve and thrive.