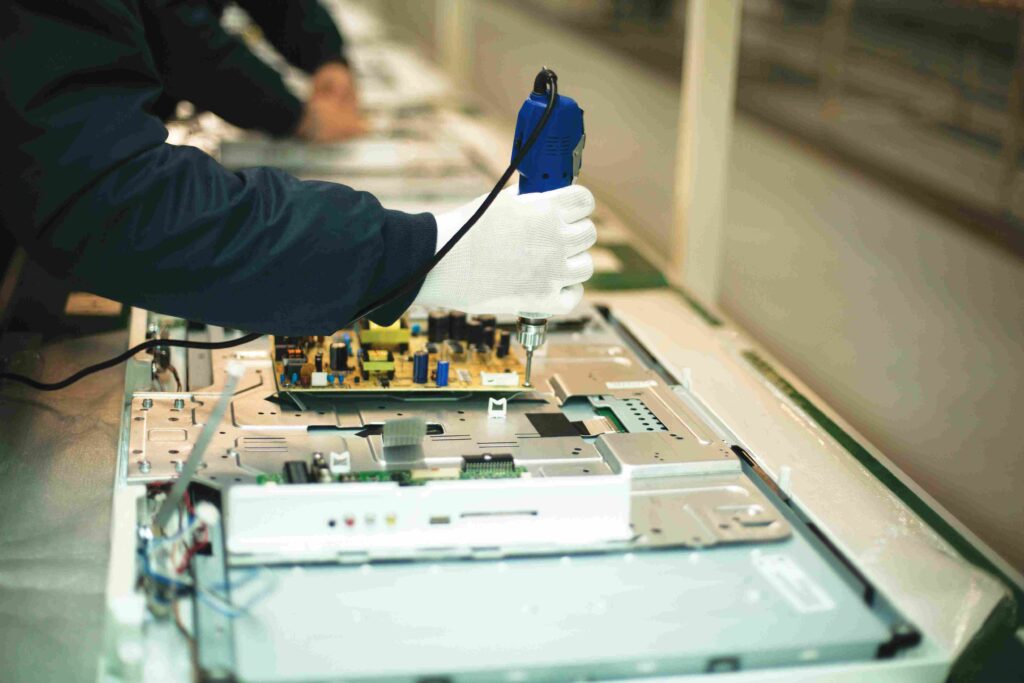
The Indian electronics and electricals industry is fast expanding, with projections suggesting the market will reach $400 billion by 2025. This growth spans sectors such as consumer electronics, automotive electronics, and industrial automation, establishing India as a leading global manufacturing hub. Alongside this, the country’s investment in semiconductor manufacturing, spurred by government initiatives like the India Semiconductor Mission, will be crucial for the future. Clean India Journal introduces the industrial cleaning in the magazine as clean manufacturing environments are essential, particularly in sensitive sectors like semiconductor production in India today.
The government has approved the Semicon India Programme, allocating ₹76,000 crore (approximately USD 10 billion) to develop the semiconductor and display manufacturing ecosystem. This initiative includes incentives for setting up semiconductor fabs, packaging units, and design centres.
In addition to government efforts, private sector investments are also contributing to the sector’s growth. For instance, Larsen & Toubro has announced plans to invest over USD 300 million to establish a fabless chip company in India, aiming to design 15 products by 2027. Furthermore, NXP Semiconductors has committed more than USD one billion to enhance its research and development efforts in India, reflecting the country’s growing importance in the global semiconductor landscape.
These investments are part of India’s broader strategy to reduce reliance on semiconductor imports and build a self-sustaining industry capable of meeting both domestic and international demand.
The Indian government’s focus on semiconductor production highlights the need for meticulous cleanliness in the manufacturing process. The fabrication of semiconductors requires highly controlled environments, as even the smallest particle of contamination can result in catastrophic failure. Cleanrooms and state-of-the-art cleaning processes will be integral to attracting foreign investment and advancing domestic capabilities in this vital industry.
Contaminants in Electronics Manufacturing
Electronics manufacturing is highly susceptible to contaminants, which can significantly impact product quality. The main contaminants include:
• Dust and Particles: These particles can be introduced by machinery, human handling, or external environmental factors. Even small amounts can cause short circuits or poor electrical connections.
• Flux Residue: Solder flux residues can remain on components after assembly, leading to electrical failure if not properly cleaned.
• Ionic Contamination: Leftover ionic particles from cleaning agents or solder flux can cause corrosion, affecting device longevity and performance.
• Fibres and Oils: Often introduced during assembly or packaging, these contaminants can interfere with the electrical functioning of the device.
• Chemical Residues: Various cleaning solvents or adhesives, if not adequately removed, can damage sensitive components.
Each of these contaminants poses a unique challenge to electronics manufacturers, making effective cleaning processes critical.
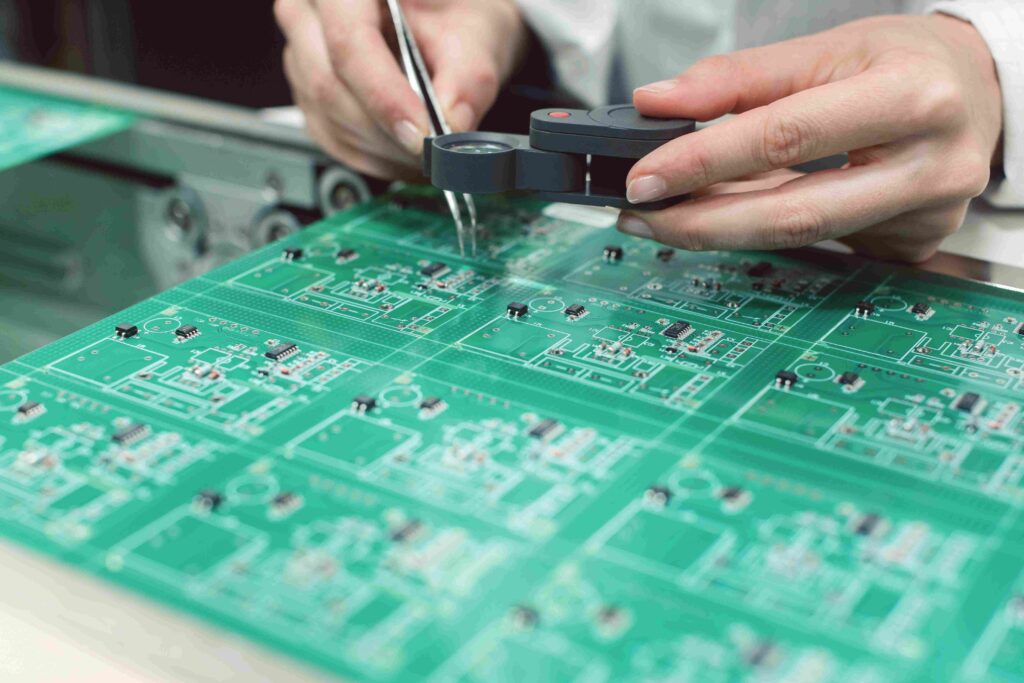
Cleaning Methods Adopted
To maintain high-quality standards and ensure the reliability of electronic products, various cleaning techniques are employed. These methods are designed to address the diverse types of contamination present during production:
1. Manual Cleaning: This involves the use of alcohol swabs, wiping, or compressed air to clean smaller components or assemblies. While effective for minor cleaning, it is labour-intensive and best suited for smaller-scale operations.
2. Aqueous Cleaning: This technique uses water-based solutions, often combined with detergents, to remove flux residues and particulate matter. Aqueous cleaning is commonly used in industries where chemical residue must be minimised.
3. Semi-Aqueous Cleaning: Combining solvents and water, this method is particularly effective for stubborn residues like flux. It removes oils and greases while being gentle enough for sensitive electronic parts.
4. Dry Cleaning: Dry cleaning methods, such as CO₂ snow cleaning, are used for delicate parts. This non-contact method involves solid CO₂ particles to remove contaminants without leaving moisture behind.
5. Plasma Cleaning: Plasma cleaning utilises ionised gases to remove organic contamination from surfaces. This technique is widely used in the electronics industry, especially for parts that require cleaning prior to coating or bonding.
6. Ultrasonic Cleaning: High-frequency sound waves are employed in ultrasonic cleaning systems to agitate a liquid medium, effectively removing contaminants from complex or small components. This method is ideal for hard-to-reach areas and offers thorough cleaning without the need for harsh chemicals.
Industrial Cleaning Solution Providers
As the complexity of electronics manufacturing increases, the need for specialised cleaning solutions becomes even more critical. Industrial cleaning service providers offer not only the necessary equipment but also the expertise to select the most effective cleaning method. These providers offer a range of advanced technologies, from ultrasonic and plasma cleaning to custom-designed systems, all of which ensure that components meet the highest cleanliness standards.
Service providers help businesses stay competitive by offering efficient cleaning solutions that meet global standards. By tailoring cleaning processes to the specific needs of each product or production stage, these companies ensure that manufacturers can consistently deliver high-quality, reliable electronic devices.
As India’s electronics sector continues to evolve, the importance of maintaining clean manufacturing environments cannot be overstated. Meeting cleanliness standards will not only help ensure product quality but also enable India to position itself as a global leader in semiconductor manufacturing and high-tech production. The adoption of advanced cleaning technologies, such as plasma and ultrasonic systems, is essential to the success of electronics manufacturing. Cleanliness is no longer just a regulatory requirement — it is a fundamental aspect of product reliability, customer satisfaction, and competitiveness in the global marketplace.