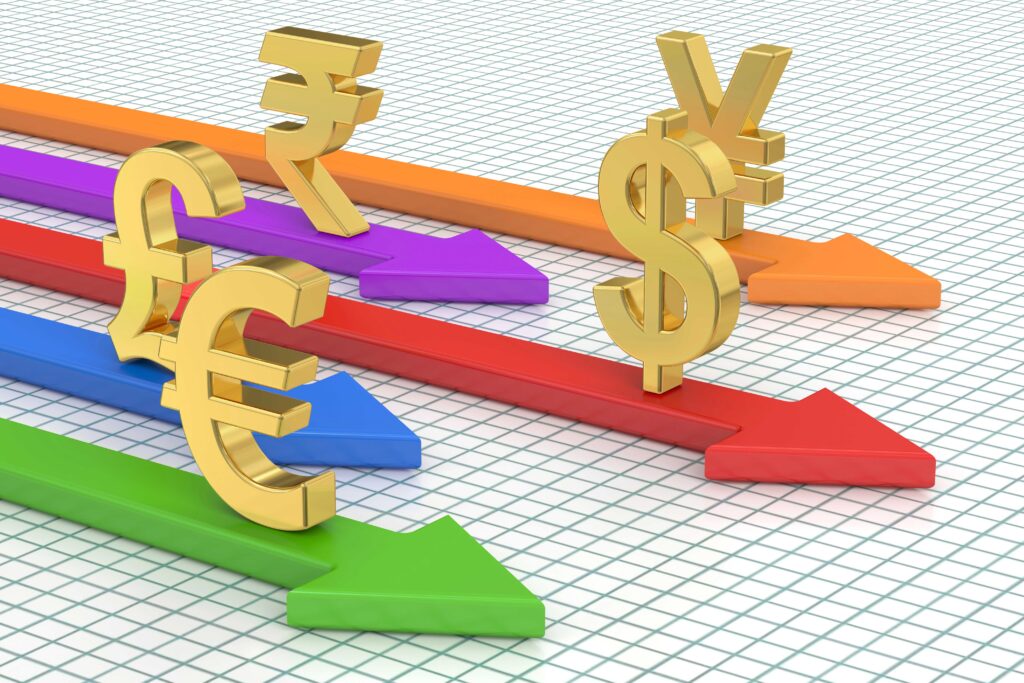
Delivering high-quality IFM services at optimal costs is a necessity considering current business trends. Meeting a company’s strict budget constraints is one of the major needs of a contemporary facilities manager. UR Uday Kumar, Managing Director of AMPS Facilities Management Services Pvt. Ltd and Afzal Khan, an FM expert, share a few top suggestions for reducing operating costs.
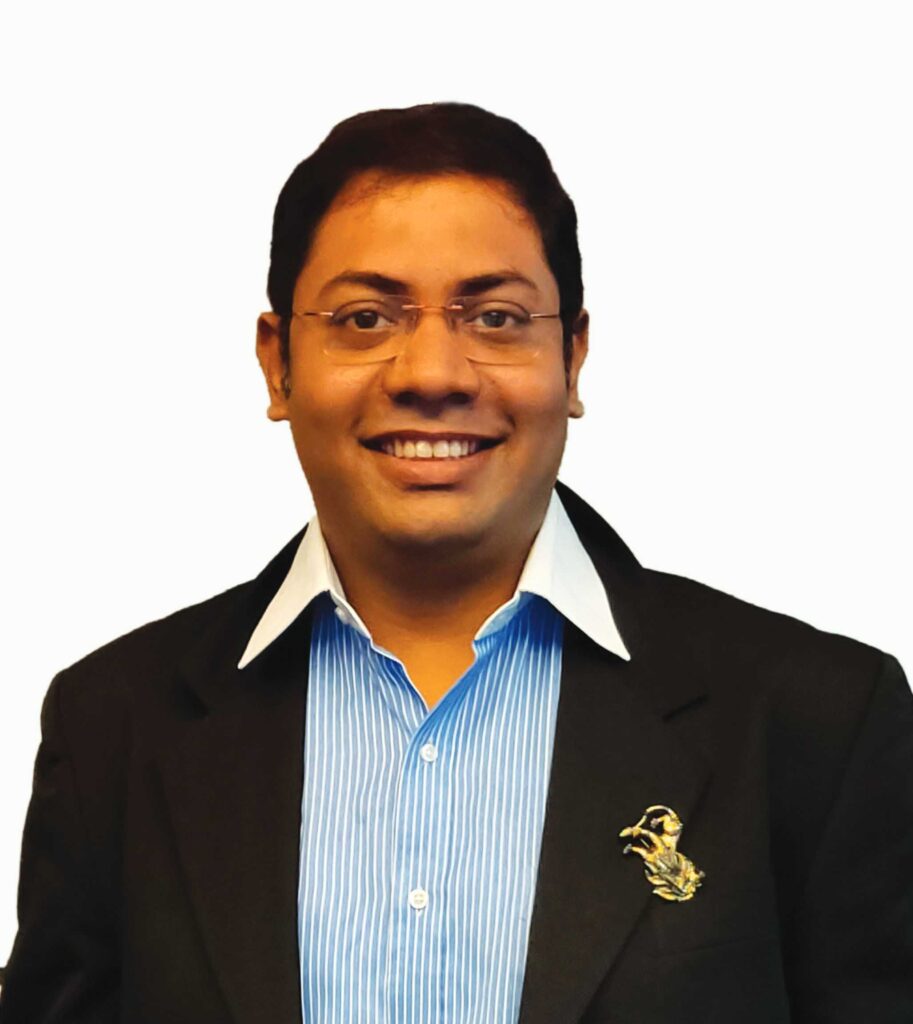
Afzal Khan, an FM expert
1. Long Term Planning (ROI Strategy): Long-term planning is necessary for one of our earlier cost-cutting strategies for facilities management. Consider the long-term return on investment (ROI) of your options while assessing your options. These would provide insight into the business’s priorities, procedures, and policies and fight to address foreseeable issues and provide a variety of solutions. When evaluating the long-term goal, many strategies can be employed to counter cost increases, and these strategies vary depending on the issue at hand.
2. Continual Improvement & Progress: If you genuinely want to reduce operating costs in your facilities, you must be exact in your efforts. Initiatives to reduce facility management costs typically require constant research and development. Although this can be a challenging effort, there may be a significant long-term reward. Make sure that a plan is established and conducted, along with the necessary KPIs. Breaking down your tasks into smaller tasks and projects would simplify the process.
3. Smart Technology and Automation: Businesses can generate considerable cost savings, increase productivity, and streamline operations by deploying the appropriate technical solutions. A Computerised Maintenance Management System (CMMS) is one tool for leveraging technology. Facilities managers may automate and centralise operations like inventory control, work order administration, and scheduling preventive maintenance with a CMMS. Facilities management can be made even more efficient by incorporating smart building technology in addition to a CMMS. Real-time monitoring of energy usage, equipment performance, and indoor air quality can be made possible via IoT sensors and automation systems.
4. Predictive/Initiative-taking Maintenance: Firstly, quality facilities management can result in substantial savings connected to assets throughout an organization. Teams that rely on reactive maintenance, i.e., waiting for a component to fail before responding to it, will typically see greater costs than those who take a preventive or predictive approach. This is due to several factors:
• Waiting for components to break before responding increases the likelihood they will need to be replaced, which is often costlier than maintenance over time.
• If a component breaks and is not spotted immediately, it can continue to drain on resources while not providing any benefit in return.
• The failure of the asset may compromise employee safety or make your business non-compliant with regulations, which may incur fines. In fact, according to Reliable Plant, predictive maintenance saves 8%-12% over preventative maintenance, and a massive 40% on reactive maintenance. By scheduling in regular servicing of assets based on your understanding of them, you can reduce the risk of failures and breakdowns and the greater costs these incidents often incur. Furthermore, consistent maintenance also goes a long way in extending the life cycles of assets. While an unmaintained HVAC system might go haywire in a few years, one that is well-treated and regularly maintained will likely last several years longer before a replacement is required. Over time, this can drastically drop the costs your company sustains on the asset management front.
6. Preventative Maintenance Plan (PMP): The goal of maintenance is to lower the expense of worn-out facilities. A maintenance programme must be devised. Additionally, it shortens the time needed to finish repairs. Not to be overlooked is the increase in operator safety. Each of them effectively increases the company’s profit margin.
7. Optimized Space Management: In a hybrid or remote working model, a lot of space is doing nothing beyond costing you money to maintain. These costs may not jump off a balance sheet as evidently as procurement costs and wastage do, but these expenses can add up quickly unless they are addressed. Through a carefully implemented space management strategy, companies can determine better ways to allocate space, dispersing people from more crowded areas and encouraging them to utilize more of the locations across the facilities. This way you can ensure no money is wasted on vacant locations.
8. Enhanced Energy Savings: A fundamental way to cut down costs is by boosting energy efficiency. This approach benefits the environment, reduces carbon emissions over time and leads to significant savings without any noticeable drop in performance. Recommending and implementing energy-saving light bulbs, double-glazing on windows and enhanced wall insulation within the facilities… It is an investment that pays back over time on a company’s energy bill. A switch to energy-saving bulbs can play a crucial role in reducing that slice of your overall costs. By introducing measures to consistently monitor and track energy usage, FM professionals can harness that data to make definitive cost-saving measures.
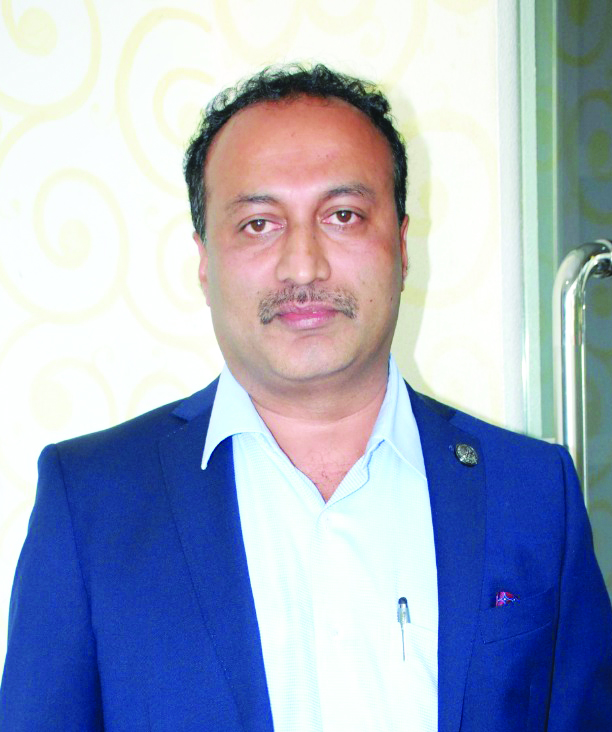
UR Uday Kumar, Managing Director of AMPS Facilities Management Services Pvt. Ltd
1. Establish maintenance processes that can be replicated: One method to cut labour expenses is to simplify your maintenance process. Internally, creating standard reproducible procedures at each level of your operation is not just one of the finest cost-cutting ideas for facility management, but it can also drastically reduce the number of labour hours necessary. This is very paramount because it helps to cut off unnecessary replicas of the same process.
2. Maintenance that is proactive: Cutting reactive maintenance is a cost-effective strategy to save money. Reactive maintenance necessitates urgent attention as well as the costs of resolving a problem that is already affecting operations and, potentially, customer and employee experiences. Regular, planned checks and maintenance, whether it is testing machinery/computer systems or inspecting the toilets to verify they are working properly, will help you avoid costly after-hours or emergency service calls. Finally, if you collaborate closely with suppliers who understand your difficulties and are open to new technology and green solutions, you will be well on your way to big cost savings for your company.
3. Implement a preventative maintenance plan (PMP): Maintenance itself is to reduce the cost of worn-out facilities which would lead to the purchase of new facilities instead of constant and effective use of an efficient facility. A maintenance schedule has to be established to reduce machine breakdowns and maintenance expenses. It also reduces the amount of time it takes for repairs to be completed. Very paramount to note is the boost in operator safety. All these successfully create a great profit margin for the organization.
4. Controlling energy efficiency: A great way to cut FM-associated costs is to lower energy consumption and make business places more energy efficient. Lighting with LED fixtures is a small part of overall energy consumption and with HVAC is the primary energy consumer taking up between 2/3rds to 3/4ths of total power consumption. This makes it compulsory to ensure HVAC is part of the energy efficiency targeting.
Office automation is the need for the hour and should be integrated at the planning stage of the workplace itself, otherwise a retrofit should be done. With automation of lights and HVAC there are tremendous benefits other than the obvious savings on energy, these include a longer lifespan for the lights and HVAC equipment which translates to lower annual replacement costs, maintenance costs and lower manpower costs. For example, a 20% reduction in energy usage directly implies that the lights and HVAC equipment have run 20% less and will therefore run 20% longer for the same maintenance costs. This reflects huge potential savings as the costs of light fixtures and HVAC equipment is substantial.
Other secondary practices that can make stores/offices more efficient include; updating lighting fixtures with more efficient bulbs, using energy efficient HVAC and other cooling equipment like refrigerators etc., adding better glazing to windows and doors, and introducing enhanced wall insulation. While this will present an immediate cost, it is an investment that will save money on cooling and energy bills in the long run. As well as being proactive and investing in energy-efficient initiatives like this, it is also vital that you consistently monitor and track energy usage across your stores. That way, facilities managers can utilize this data to introduce informed cost-saving measures in the future. In some locations, energy efficient initiatives like this can actually entitle businesses to tax cuts or other monetary incentives. However, it is worth noting that this is very much location-dependent and FMs would have to do research in the local area to find out what (if anything) they are entitled to.
5. Control your energy use: Manual and paper administration costs time and the environment. Shifting to electronic facilities management can eliminate a whole layer of form filling and paper bureaucracy that generates waste. But CAFMs can also help you monitor key energy and asset KPIs to meet tougher environmental regulations.
• Extend asset lifecycle: Using PPM software can reduce failure rate and the need to scrap equipment.
• Use FM data to maintain, monitor and optimise energy consumption of critical assets
• Plan the movement of engineers and contractors to reduce carbon footprint
• Integrate Building Management and CAFM systems to access and control more energy use data
6. Retrofit existing building systems: Retrofitting often involves modifications to existing commercial buildings that may improve energy efficiency and decrease energy demand. Energy-efficiency retrofits can reduce the operational costs, particularly in older buildings, as well as help to attract tenants and gain a market edge.
7. Utilize an IoT-enabled monitoring system with your CMMS: If you are using a building system to report changes after implementing energy savings initiatives, then your equipment needs to be audited regularly to make sure that the equipment is not overworking itself. This is critical to categories of equipment like HVAC. Auditing set points daily through a remote monitoring platform allows you to automatically reset your equipment set points. This ensures your HVAC is running at the correct temperature.
• Analyze your current energy consumption
• Itemize your building’s energy usage
• Seek out stable, long-term energy costs
• Upgrade your lighting